Breathing clean air shouldn’t be a luxury in workplaces, but for many facilities, that’s far from reality. Dust-related problems don’t just make things look grimy—they harm health, damage equipment, and reduce productivity. Ignoring the issue isn’t just bad management; it’s dangerous. Every facility needs a plan to tackle air quality issues head-on, keeping employees and equipment safe.
Key Points:
- Dust compromises worker safety and health.
- Effective air quality measures improve productivity.
- Proper systems prevent regulatory penalties.
- Control systems like baghouses offer cost-effective solutions.
Maximizing Efficiency with Precise Baghouse Systems
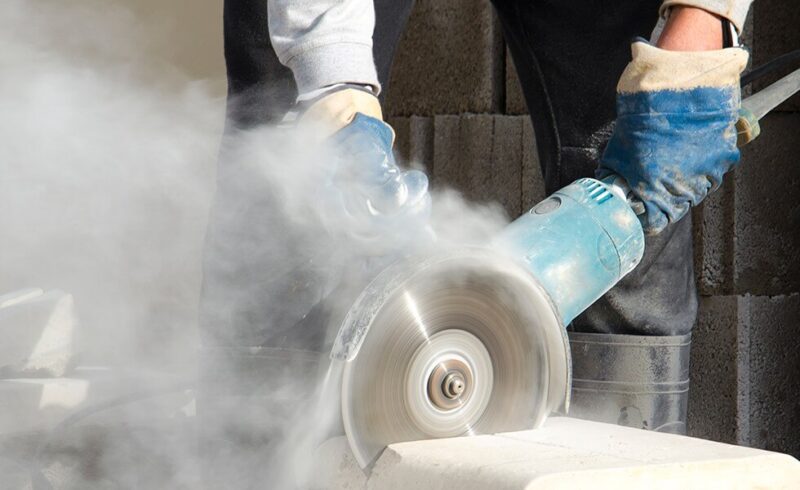
Choosing the right dust control method is critical for maintaining a safe and productive workplace. A well-designed baghouse system offers an effective way to capture harmful particulates, but ensuring it meets your facility’s specific needs requires careful planning. Conducting a baghouse calculation helps determine the optimal system size and configuration, balancing cost and performance.
Key considerations for baghouse systems include:
- Particle Type and Volume: Understand the nature and quantity of dust generated to select an appropriate filtration system.
- System Design: Ensure proper sizing and airflow capacity for efficient performance without overloading.
- Regulatory Compliance: Meet air quality standards to avoid penalties and maintain worker safety.
- Maintenance Needs: Evaluate ease of filter replacement and overall upkeep to reduce long-term operational costs.
The Health Hazards Nobody Talks About
Breathing dust particles is like inhaling a steady stream of micro-invaders. They sneak into the lungs, causing irritation, allergies, and more severe conditions like silicosis or chronic bronchitis. Workers who handle fine particles over long periods face the greatest risks.
Here’s why it matters:
- Respiratory issues: Even non-toxic dust can cause breathing troubles.
- Skin irritation: Airborne particles settle on exposed skin, creating rashes or dermatitis.
- Toxic exposure: Facilities working with hazardous materials face dual risks—dust and chemical particles in the air.
Ignoring health risks isn’t an option. Employees will voice concerns or, worse, quit when conditions are unsafe.
Why Air Quality Impacts Productivity
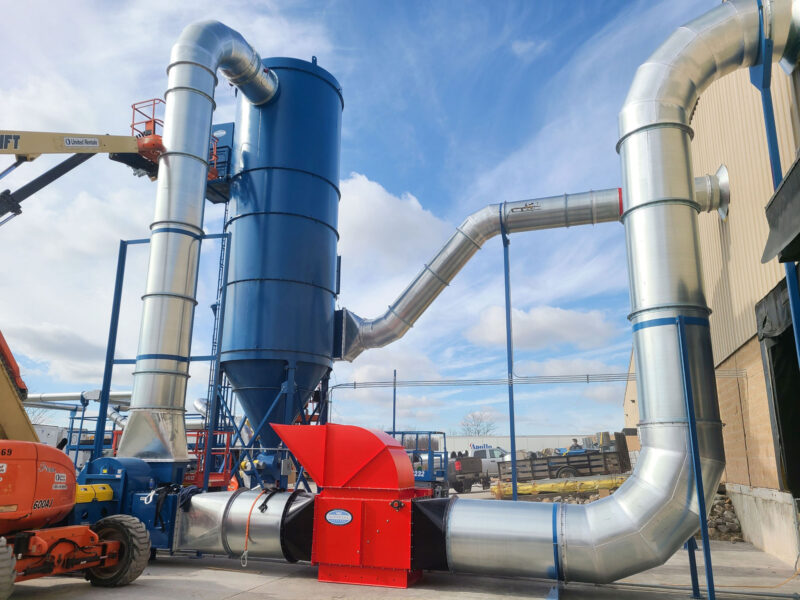
When workers breathe easier, they work better. Airborne particles aren’t just health hazards; they slow everything down. Machines jam, filters clog, and downtime eats into profits. Facilities without proper systems like baghouse filters often deal with frequent breakdowns, which cost more than preventive measures.
Dust clouds also lead to:
- Reduced visibility, increasing accident risks.
- Contaminated products in food or pharmaceutical settings.
- Regulatory penalties for non-compliance.
Effective air management systems do more than clean the air—they reduce maintenance costs and improve workflow.
The Role of Baghouses in Dust Control
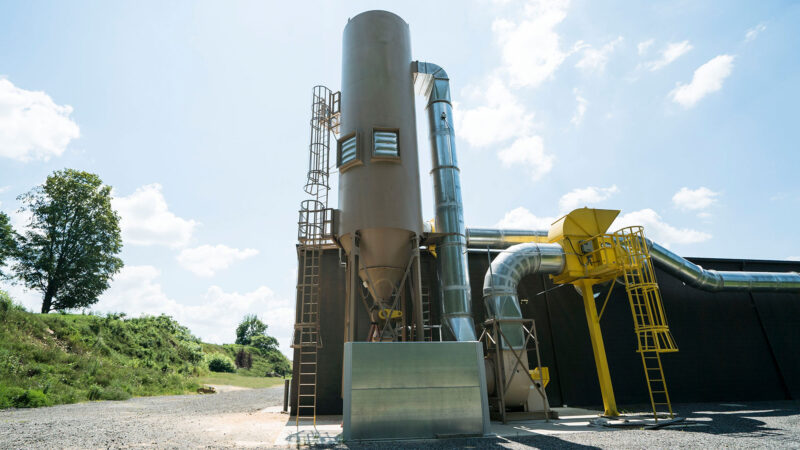
Baghouses are powerful tools for improving air quality. They trap dust particles before they escape into the workplace. Facilities using baghouses benefit from cleaner air, healthier employees, and reduced equipment wear.
However, choosing the right system requires careful planning. Factors like baghouse cost estimates, baghouse calculations, and filter specifications determine success.
How to Calculate Baghouse Efficiency:
- Estimate operational needs: A baghouse cost estimate helps align budgets with goals.
- Run airflow calculations: Use a baghouse calculation example to determine filter size.
- Adjust for contaminants: Consider unique facility needs to calculate baghouse CFM.
- Test performance regularly: Adjust baghouse filter calculations based on results.
Compliance Isn’t Optional
Workplace safety laws require facilities to meet specific air quality standards. Failing to do so triggers costly fines and legal challenges. A proactive approach ensures compliance and protects reputations.
Dust control systems aren’t just solutions—they’re investments in operational integrity. Facilities operating without them risk everything, from penalties to production delays.
Tips for Maintaining Air Quality Systems
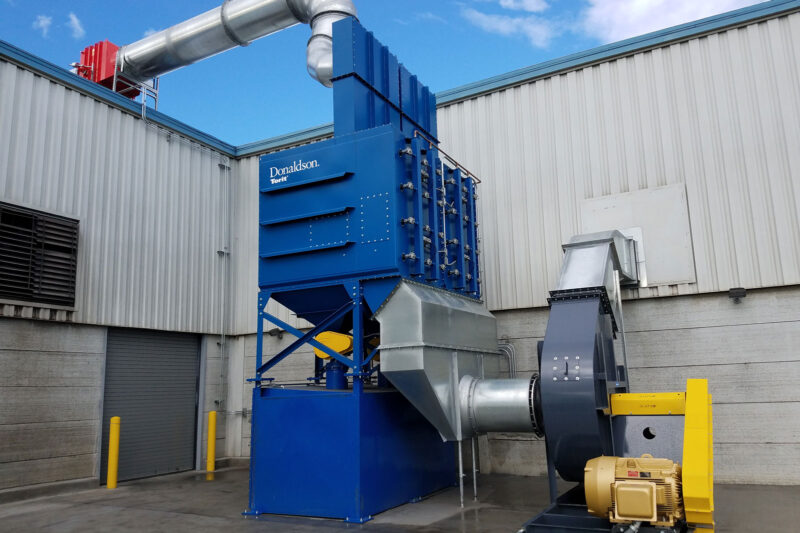
- Regular inspections: Check systems weekly for clogs or wear.
- Employee training: Workers should know how to operate air management equipment safely.
- Filter replacements: Replace filters on schedule to maintain peak performance.
- System upgrades: Evaluate baghouse calculation examples to upgrade outdated units.
- Monitor air quality: Use sensors to track improvements and identify problem areas.
Real Benefits of Dust Control Solutions
Facilities prioritizing air quality enjoy tangible benefits:
- Fewer health complaints: Workers stay productive with fewer sick days.
- Longer equipment life: Machines work better with clean air.
- Regulatory ease: Compliance becomes straightforward with reliable systems.
Baghouse Systems: A Cost-Effective Solution
The cost of ignoring air quality far outweighs investing in the right equipment. Calculating baghouse CFM ensures systems meet demands without overloading. A solid baghouse cost estimate helps plan budgets, and precise calculations reduce unnecessary spending.
Facilities equipped with baghouses see long-term gains, from happier employees to reduced repair bills. Don’t wait for a crisis before acting.
Hidden Costs of Poor Air Quality
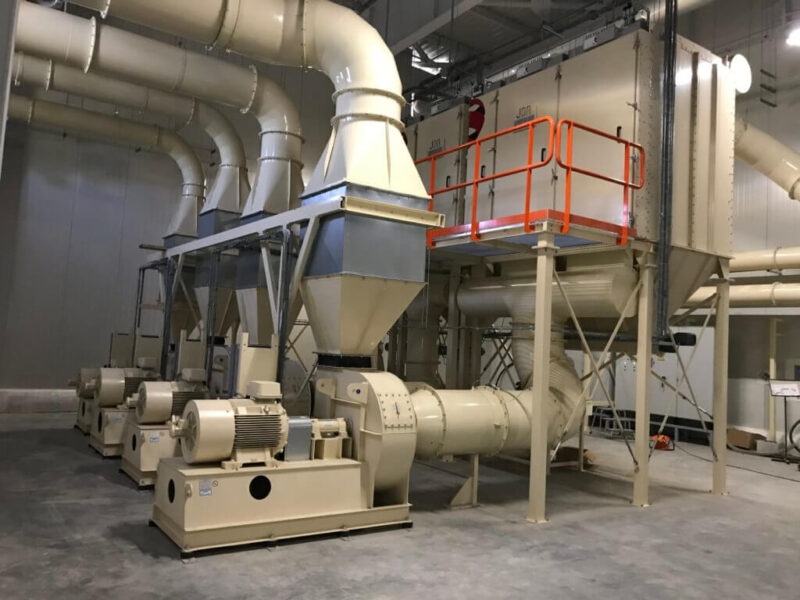
Neglecting air quality doesn’t just harm workers—it drains resources in ways many facilities overlook. Equipment exposed to airborne particles requires more frequent maintenance, and replacement costs pile up fast. Dust accumulation reduces the lifespan of everything, from HVAC systems to production machinery.
Another often-overlooked expense is product contamination. For facilities in industries like pharmaceuticals or food processing, dust can ruin batches, leading to wasted materials and financial losses. Customers also lose trust when quality slips.
Investing in proper air management systems reduces these hidden costs while boosting long-term profitability.
How to Choose the Right Dust Control System
Not every facility has the same air quality challenges, so a one-size-fits-all solution doesn’t work. Start by analyzing the specific needs of your space. Facilities with heavy particle loads might need advanced baghouse systems, while smaller spaces might require simpler filtration units.
Key Factors to Consider:
- Dust type: Fine particles require different filters compared to larger debris.
- Airflow demands: Use baghouse calculations to determine the ideal system size.
- Space availability: Ensure equipment fits seamlessly into the existing layout.
- Maintenance needs: Choose systems that are easy to clean and service regularly.
A well-planned system ensures cleaner air, lower costs, and happier workers. Don’t rush the process—evaluate every option before committing to a solution.
Conclusion
Ignoring air quality risks in industrial spaces leads to health problems, lost productivity, and legal trouble. Facilities need dust control measures to protect workers and maintain operational efficiency. Systems like baghouses deliver clean air and peace of mind, making them essential investments.
Improving air quality isn’t just smart; it’s necessary for every facility looking to thrive in the long run.