Warehouses buzz with activity – workers moving about swiftly, machinery operating, vehicles being loaded. But where there’s hustle and bustle, there’s also safety risks. warehouse hazards and accidents frequently lead to worker injuries, damaged goods, and work disruptions.
No doubt keeping your operations running efficiently is important. However, as per safety experts at Advanced Warehouse Structures, it should never come at the cost of safety. Protecting your staff needs to remain the top priority at all times.
This article will provide an overview of the most frequent warehouse dangers and offer practical, realistic tips to help avoid them. Let’s discuss how you can make your warehouse a secure place for your team.
Poor Layout Increases Risks
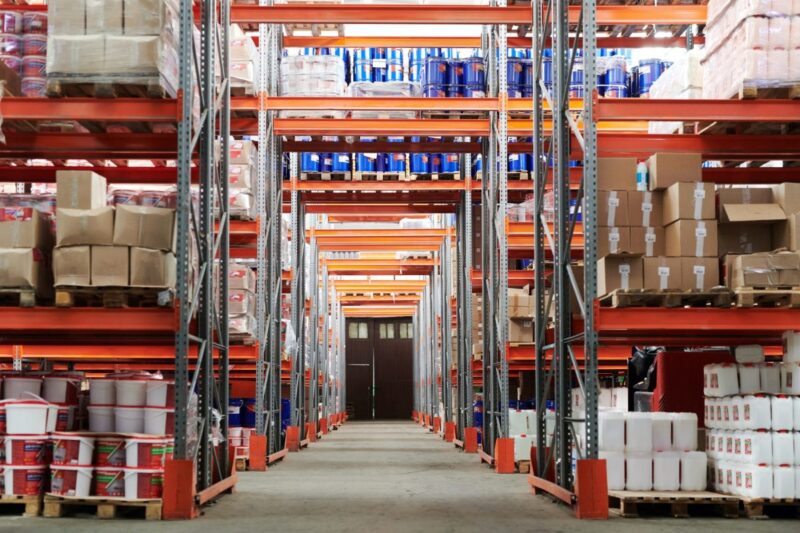
The layout of your warehouse has a significant impact on efficiency as well as safety, productivity, and efficiency. A well-organized layout will help with the need for storage and flow. The items are organized to prevent the hassle of daily tasks and make it more efficient.
In addition, poor design creates traffic jams for workers which can cause delays in finding the right stock and maneuvering around narrow space. This increases the risk of accidents.
Review your layout regularly to spot areas that are in need of attention. Find areas that are frequent collisions. Moving the aisles to allow for wider ones and a better system of organization decreases the risks considerably.
Slips, Trips, and Falls
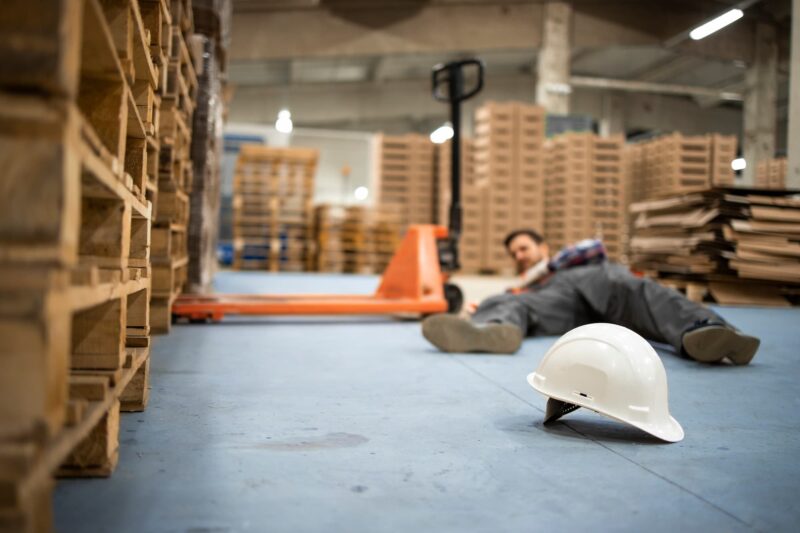
When workers are moving fast to complete their tasks It’s possible to allow a momentary absence of attention that could result in an injury-inducing fall. Accidents, dirty aisles and uneven floors are all common causes of slips and falls that can lead to accidents.
Reduce the risk of accidents by quickly cleaning up spills, keeping paths free of obstacles and marking slippery surfaces with signs warning of slickness as well as installing anti-slip flooring in places that are frequented by traffic, and providing sufficient lighting to spot the dangers of tripping. A quick clean-up and tidy environment prevents numerous falls.
The falling items from Overhead Storage
The falling of objects from overhead shelving and storage areas could result in injuries and damage to items below. The overloaded shelves or the improper placement of heavy objects up high increase the risk of injury.
To prevent falling object accidents, make sure you don’t exceed the posted weight limits for shelves. Restraints are used to hold errant objects and stack the heaviest items on the bottom shelves, and educate employees properly to ensure safe lifting and lowering overhead loads.
The time spent organizing storage spaces in accordance to size and weight could help avoid many falls.
Hazards to docks and loading
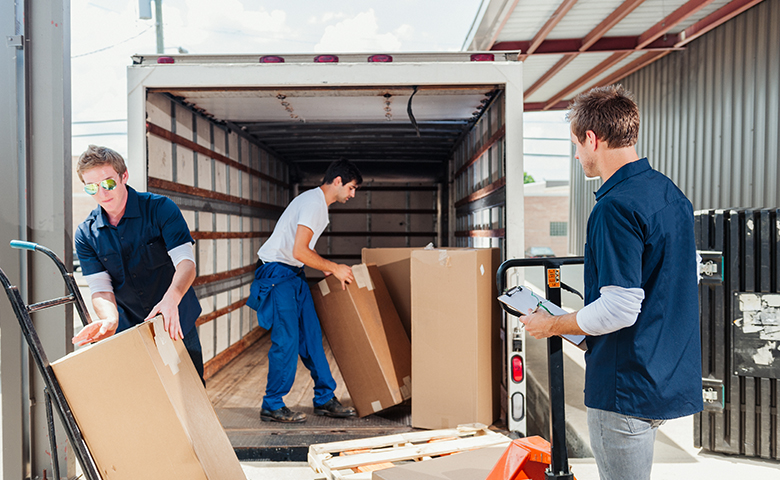
The docks at loading are particularly dangerous for injuries. Docks that are loaded are highly-active where large vehicles are able to move around as workers perform their duties. Forklift accidents, truck back up, and material handling are quite common.
There are many methods of reducing risks at loading docks, for example the installation of alert lights on the dock’s doors to warn to truck arrivals, creating free lanes for forklifts from walkways, making sure pedestrians and drivers maintain eye contact, ensuring dock plates in good condition and having a qualified spotter to guide vehicles and coordinate their activities. Being vigilant in loading zones avoids a lot of accidents and collisions.
The absence of Adequate Safety Rules and Training
Insufficient training on safety procedures makes workers ill-equipped to complete tasks safely. They may not be aware of dangers and the proper operation of machinery or handle material safely. It’s essential to prepare all new hires in safety procedures and policies, check on key safety procedures regularly with the veteran employees to refresh their knowledge base. The comprehensive safety training provides employees with the necessary information to be secure on the job and complete tasks in a safe manner.
Disorganized Storage Spaces
Lack of storage space can lead to messy, dangerous conditions such as shelves overstacked and objects that block pathways. Unorganized spaces also affect productivity.
Make the most of storage space by categorizing your inventory in a smart way and installing sturdy shelving to hold loads, and adding modular storage such as mezzanines to make use of vertical space that isn’t being used as well as keeping areas free of obstructions.
A well-organized storage area drastically reduces risk of accidents and allows stock to be easily available.
Hazardous Substances
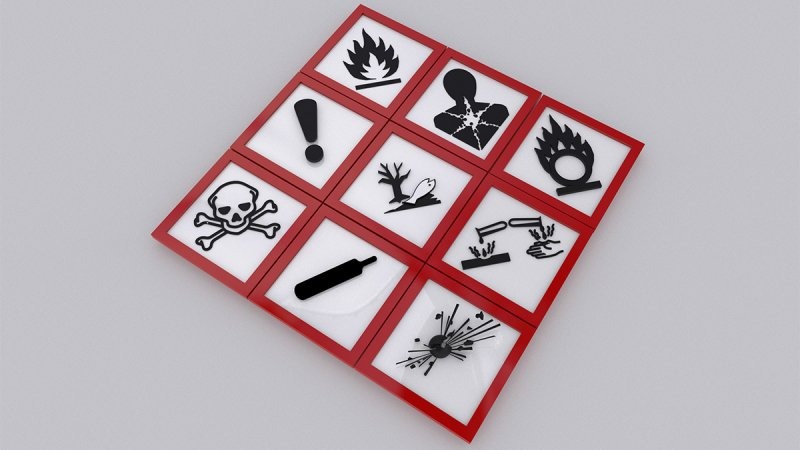
Warehouses typically contain paints, adhesives and chemicals and solvents, as well as other dangerous substances. Handling them improperly can pose risks of burns, poisoning or even explosions.
A few tips to ensure that staff are secure when handling hazardous materials are labeling and identifying hazardous materials, ensuring safe handling, transportation and disposal, keeping in sealed containers that are suitable for restricted areas, which requires the wearing of personal safety equipment and putting emergency eyewash and shower stations nearby.
Understanding the risks unique to every chemical is a way to reduce the risk of accidents.
Conclusion
By being vigilant and making safety a top value, you can significantly reduce accidents in your warehouse. Your diligence protects not only your facility and operations, but most importantly, your staff. Their safety should always come first. Staying alert and proactive keeps a warehouse hazard-free.
Related Posts:
- Common Types of Maritime Accidents and How to Avoid Them
- Top PPC Trends to Watch in 2025: Staying Ahead of…
- How to Check SD Card Health on Windows - Keep Your Data Safe
- Are DLL Files Dangerous? Identifying Safe vs. Malicious DLLs
- Why Invest in a Warehouse Intercom System?
- Server Downtime: Common Causes and How to Prevent Them